How to Construct the Cause-and-Effect Diagram for a Formal RCFA Analysis
Constructing the Cause-and-Effect Diagram
Remember, the purpose of a Cause-and-Effect Diagram is to identify the causes or conditions that produces an effect. By understanding this, we can then identify the relationships (links) between the different causes and contributing conditions and then determine the most effective way of breaking the link(s) in the chain to prevent the Undesirable Event. Failures can be caused by a combination (chain) of events or a system of causes and conditions; there is not necessarily one correct answer to the problem.
After defining the problem details, the next step in the process is to visually map out all the contributing factors and the relationships that exist between the various causes and the effects.
The Verification Process
- To develop a Cause-and-Effect hierarchy for a failure, navigate to the Cause and Effects Diagram tab.
- The Undesirable event or Failure node will already be added as the starting point of the Cause-and-Effect hierarchy. We always have to start with the event we want to prevent from reoccurring and work backwards in time.
- Once your Diagram is saved the Undesirable Event will be marked with the letters (UE) to indicate the beginning of the process. Note that the system auto saves your work.
- Start adding the possible Causes that could have led to the Undesirable Event by selecting the Cause node from the side panel.
- Double Click in the middle of the Cause node to give the Cause a Name and click outside the field so the name can be saved. The user can add as many Causes as is necessary.
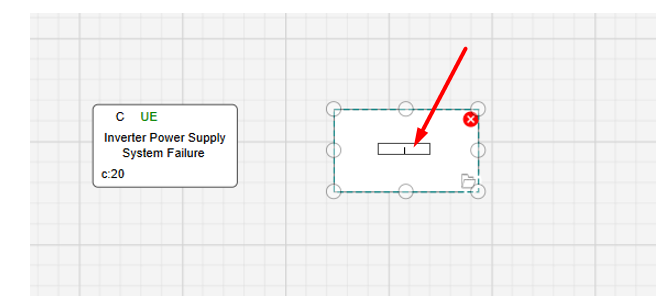
- Use the AND/OR Gates by dragging and dropping them on the diagram where they are applicable to illustrate the flow of the Root Cause Identification process.
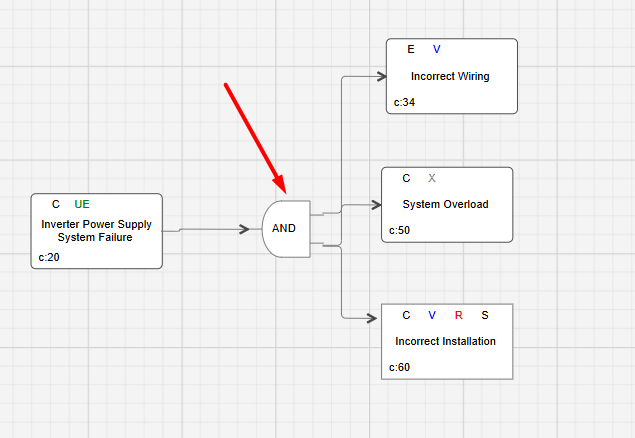
- AND- The connector AND is used to indicate that multiple conditions or factors must all occur simuktaneously for the failure or effect to happen. It implies that the failure is not caused by a single event but rather by a combination of several causes working together.
- OR- The connector OR indicates that the failure or effect can occur if any one of the connected causes happens. It means that multiple factors may independently lead to the same failure, but only one needs to occur for the failure to be triggered.
- Use the connector by dragging and dropping it in the applicable spot on the diagram to indicate the relationships between the different Causes.
- Once the connector is placed, select it until the two nodes on each end are visible. Drag the line to connect a parent to a gate or directly to a Cause if there is only 1 parent and 1 cause.
- If you wish to remove the Cause, simply click on the cancel icon as illustrated below and the entire node will be removed from the diagram.
- Click on the Cause Node such that a little file icon appears on the bottom right corner to capture the verification details.
- A verification pop-up will appear.
- Under the Cause Analysis tab, use the dropdown menu to classify the Cause.
- Cause: A cause is a condition that produces an effect; eliminating a cause(s) will eliminate the effect.
- External Conditions: This refers to factors outside the immediate system or process that could have contributed to a failure. These conditions are not part of the equipment, design, or operational procedures, but they can still have significant impacts on performance, reliability, or safety.
- Secondary Protection: This refers to additional safety mechanisms or backup systems designed to protect equipment or processes if the primary protection system fails.
- The below highlighted fields are read-only fields that have information captured during the beginning stages of the RCFA analysis.
- On the Parent field dropdown, If the user in on the first level of the hierarchy, the cause will not have a parent. However, the user can select a parent from the dropdown menu if as they continue to build the Cause-and-Effect tree.
- Capture a Description regarding the cause.
- Click the Save button.
- Now, click the Verification tab.
- The Cause field will be auto populated from information captured from the analysis.
- Select the method of verification from the dropdown menu. Every Cause Category will have different verification techniques. These will be identified here, and the description field will automatically be captured depending on the selection however this does not prevent the user from capturing a unique description.
- Capture the Confidence Percentage.
- Capture any Supporting Information.
- Assign the verification task to the Responsible Person by selecting from the dropdown menu and use the calendar icon to assign a Target Date.
- Verify if the Cause needs further analysis by selecting Yes or No from the dropdown menu. If the Cause is verified No, this means that the process ends there. The Root Cause Verification and Classifications sections will disappear. The Cause will be indicated by the letter (X) on the Cause-and-Effect Diagram.
- Capture supporting information.
- Use the calendar icon to capture the Target Date.
- Click Save if the Cause is verified as No and the verification pop-up will disappear.
- If the Cause is verified Yes, the Cause will be indicated by the letter (V) on the Cause-and-Effect Diagram.
- Navigate to the Root Cause Verification section.
- Indicate if the Cause is a Root Cause or not by selecting Yes or No from the dropdown menu.
- If the Cause is identified to be a Root Cause, this will be indicated by the letter (R) on the Cause-and-Effect Diagram. Remember, it is possible to have more than one Root Cause.
- Navigate to the classifications section and select from the different cause categories. The Description will automatically be captured based on the selection.
Root Cause Categories/Classifications
Cause and Effect analysis should include all categories of possible causes. These include physical causes, human causes, and organizational / procedural (latent) causes.
- Physical Causes: These consist of erosion, corrosion, abrasion (mechanical wear and tear), fatigue and oxidation.
- Human Causes: These consist of anthropometric, human sensory, physiological, and psychological factors.
- Organizational/Procedural (Latent) Causes: These consist of operational, maintenance and purchasing procedures, people’s attitude, lack of
proper training, and working culture and environment.
- Capture any supporting documentation.
- Click Save.
The Solution Identification Process
- Navigate to the Effective Solutions tab.
- A list of possible solutions will be listed based on the cause classification.
- Select the applicable solution and click the Questions button. A pop-up with a list of questions related to the selected solution will appear.
- Answer the questionnaire by selecting the answers from the dropdown. User the directional arrows to go to the next or previous question.
- Capture Supporting Information for each question if any.
- Click the Done button at the bottom of the pop-up window to close the pop-up.
- The text will change color to indicate different statuses about the solution.
- Green- Completed Solution
- Blue- Incomplete Solution
- Red- Not a Solution
- Now select the Details button to capture the Justification for the identified solution.
- Capture the Description of the solution details.
- Expand the Justification section and capture the answers to the Justification questions.
- Expand the Responsible Person section. This section contains the details of the people who must review and approve the identified solutions.
- Select the Responsible Person using the dropdown menu. The capacity of the Responsible Person will automatically be added on the post field.
- Use the calendar icon to capture the Target Date for review.
- Now select the Approval person using the dropdown menu and the post field will also be captured automatically.
- Use the calendar icon to select the Completion Date.
- Click the Done button to close the pop-up window.
- Check the completed checkbox at the bottom of the solutions.
- Click Save and exit the verification pop-up. You have now reached the end of the formal RCFA analysis.
- The Cause will now display an additional letter (S) to indicate that a solution to the Root Cause has been completed.
- If the solution is not relevant, select the Delete button.
- Confirm the Delete action by clicking Delete on the pop-up. if this action was not intended, select Cancel.
Related Articles
Root Cause Failure Analysis (RCFA) Overview
Root Cause Failure Analysis Overview RCFA is a systematic and structured process to identify the most effective solutions to eliminate completely, or to manage to the satisfaction of the asset owner, the causes of failures, events or incidents that ...
How to Add Problem Details to a Formal RCFA Analysis
Adding the Problem Details The Problem Details are the functional description of the Undesirable Event/Failure. It includes: The definition of the function that was affected by the undesirable event - What is the equipment, process or system supposed ...
How to Define an Undesirable Event for a Formal RCFA Analysis
Completing the Problem Statement and Definition The Undesirable Event is a specific Failure, event, or incident or a chronic condition. There are two main categories that trigger an undesirable event namely the sporadic events and chronic events. ...
How to Complete an RCM2™ Analysis
The RCM2™ Methodology The RCM2™ methodology is a process used to determine what must be done to an asset to preserve its functions (while minimizing or avoiding failure consequences). Prior to starting an analysis, a trained facilitator or asset ...
How to Complete a New RCS Repairable Interval Reliability Analysis
How to Complete a New Repairable Interval Reliability Analysis A repairable Interval Reliability analysis is conducted to determine the probability of not running out of stock at any moment over a specified period of time, such as one year. This can ...