Completing the Policy Worksheet
The “Policy Worksheet” is associated with the specific Risk Management Strategy that is defined for each identified Failure Mode during the analysis of the Functions and Failed States. Depending on the answers to the "Decision Diagram", ACTOR will generate the policy outcome as shown in the below examples:
NB* It is important to note that the Worth Doing Tab in the RCM3™ analysis workflow will become active only if the policy supports it. The system will notify the user if a policy does not support Worth Doing as illustrated below:
On-Condition Maintenance or OCM Tasks (Supports Worth Doing)
Tasks designed to detect Potential Failures are known as On-Condition tasks. On-Condition tasks are so called because the items that are inspected are left in service on the condition that they continue to meet specified performance standards.
How to complete the OCM Policy Details:
- The Information Details section is information carried over from the Information Worksheet.
- The Policy Type will be pre-selected based on the answers from the Decision Diagram.
- In the dropdown, select the Policy Sub Type. Like any other dropdown list in ACTOR, these are records from the Base file. The user however is able to create new or update existing policy sub-types which will also subsequently be added to the Base file. This method of adding or updating records is consistent throughout ACTOR for all the dropdowns.
- Capture the Plant Status.
- Capture the Equipment Status.
- Capture the Potential Failure or P-F Condition. This is the identifiable condition that indicates that a functional failure is either about to occur on in the process of occurring.
- Capture the P-F Interval: This is the minimum level likely to elapse between the discovery of a potential failure and the occurrence of a functional failure. It describes how often an On-Condition task must be performed.
NB* The system will automatically populate the Policy Interval and the Policy Interval UOM as soon as the P-F Interval and P-F Interval UOM fields are captured. This does not however prevent the user from capturing custom data if required.
- Capture the P-F interval Unit of Measure or UOM- This describes the frequency at which the On- Condition task must be carried out. E.g. Days, weeks, months, years etc.
- Capture the Technology.
- Select the Standard Policy and the Standard Policy details will automatically be populated.
- Update the Policy interval if necessary.
- Update the Policy interval UOM if necessary.
Adding and Deleting Trades
NB* All Policies where trades need to be added will follow these same steps.
- Select the Trade from the dropdown menu.
- Capture the Quantity by double clicking so that the fields become active for the user to enter data.
- Capture the Duration by double clicking so that the fields become active for the user to enter data.
- The man hours will automatically be calculated.
- Select the Save button and the Man Hours will be calculated.
- Select the bin icon if you wish to remove or delete a Trade.
Adding and Deleting One-Time Changes
NB* All Policies where One-Time Changes need to be added will follow these same steps.
A One-Time Change will be considered to reduce the risk in the even that no proactive task can be found that would do so on its own or when a combination of tasks will also not accomplish this. For failures that impact safety and the environment, the One-Time Change will be compulsory.
- Select the One-Time Change from the dropdown menu.
- Capture the One-Time Change details by double clicking on the field so that the fields become active for the user to enter data.
- Click the main Save.
- Select the bin icon to delete a One-Time Change
Completing Policy Indicators
NB* All Policies where Policy Indicators need to be added will follow these same steps.
If evidence can be found that something is in the final stages of failure, it may be possible to take action to prevent it from failing completely and/or to avoid the consequences. These are recorded in the Policy Indicator section of the On-Condition Task in ACTOR.
- Most times this section is collapsed in the Policy Worksheet. Expand the Policy Indicator section and select the Indicator from the dropdown menu.
- Depending on the selection, the Indicator UOM, Description and Indicator Type will automatically be populated as this is data from the Base files.
- Capture the Indicator Limits
- Capture the Indicator Action
Capturing the Revised Risk
NB* All Policies where Revised Risks need to be added will follow these same steps.
The Revised Risk process is a process of determining what needs to be done to reduce intolerable risks to a tolerable level in a cost-effective way using Risk Management Strategies.
NB* The Inherent Risk must have been captured in the Information Worksheet before a Revised Risk can be captured.
- Select the "Revise Risk" button and a pop-up will appear.
- Click the "Select from Risk Matrix" button as a shortcut for completing the Revised Risk.
- Select the Consequence Category and determine the Likelihood/Probability of the Potential Failure occurring after implementation of the Risk Mitigation strategies. ACTOR will automatically calculate the Risk Ranking.
- The Revised Risk Ranking is reviewed in comparison to the Inherent Risk to assess the effectiveness of the Risk Mitigation strategies.
- The user can also manually capture the Revised Risk by selecting the Probability from the dropdown menu. The Probability Description will be automatically populated.
- Select the Consequence from the dropdown menu.
- ACTOR will automatically pull the Loss Type values from the Inherent Risk and calculate the Risk Ranking.
- Click the "Done" button and the Revised Risk will be saved successfully. This action will also close the pop-up window.
- Capture any Notes in the Notes field.
- Select the main SAVE to ensure that all the Policy Details are saved.
Preventative Maintenance Tasks or PREV (Supports Worth Doing)
In terms of physical asset management, it is possible to reduce the probability of the failure event happening through preventing the item from getting into a failed state. Scheduled Restoration and Scheduled Discard Tasks are two preventative options that can be applied to reduce the consequences of the failure.
How to complete the PREV Policy Details:
- The analysis summary will already be populated with details captured in the Analysis Detail.
- The Information Details section is information carried over from the Information Worksheet.
- The Policy Type will be pre-selected based on the answers from the Decision Diagram.
- Select the Policy Sub Type.
- Select the Plant Status.
- Select the equipment status.
- Capture the Useful Life
- Select the Useful Life UOM
OREST Integration Explained:
The Optimal Replacement of Equipment or OREST module previously known as the Weibull module, assist users to analyze reliability data to obtain the optimal preventive replacement policy in three scenarios: deterministic replacement, age preventive replacement and constant interval preventive replacement. The integration from RCM to OREST has been created in ACTOR to enable users to easily perform a trend analysis of failure data for the identified Failure Mode simultaneously whilst defining the appropriate preventative replacement policy.
- If a user has an OREST module license, they can select the OREST button which will redirect the user to the OREST module. The outcomes of the OREST analysis will be reflected in RCM.
- If the user is not licensed, this button will be unselectable.
- Select the Standard Policy and the Standard Policy Detail will automatically be populated.
- Capture the Policy Interval.
- Select the Policy Interval UOM.
- Capture Trades.
- Capture One Time Changes if necessary.
- Capture the Revised Risk.
- Capture Additional Notes.
- Click Save.
Combination of Tasks (COT) Policy type
For a very small number of evident or hidden failure modes that have safety, or environmental consequences and a task cannot be found that on its own reduces the risk to a tolerably low level, a combination of tasks usually from two different task categories is carried out.
How to complete the COT Policy Details:
- The Analysis Summary is information carried over from the Analysis Detail.
- The Information Details section is information carried over from the Information Worksheet.
Select a Policy Type from the dropdown menu.
The selected Policy Type will be added to the grid.
Double click on each Policy and complete the policy details. Refer to the above steps on how to complete a PREV or OCM Policy.
- Select the bin icon to delete or remove a policy.
- Click Save.
Failure Finding Task (FT) Policy Type
Failure Finding Tasks entail checking hidden functions periodically to determine whether they have failed. These tasks seek to increase the reliability and availability of the protective device (where the protective device is protected by one or more protective devices) to reduce the risks associated with its failure to a tolerable level.
How to complete FT Policy Details:
- The analysis summary will already be populated with details captured in the Analysis Detail.
- The Policy Type will be pre-selected based on the answers from the Decision Diagram.
- Select the Policy Sub Type.
- Select the Plant Status.
- Select the Equipment Status.
Calculating the Initial Interval using the less Rigorous Method
- Select the Initial interval button for a less rigorous calculation and a pop-up window will appear.
- Capture the Required Availability. This is the probability that the equipment will perform its task. The Required Availability value in ACTOR is linked to the Safety Integrity Levels (SIL). When the user captures the required availability, ACTOR uses this value to determine the Safety Integrity Levels based on the IEC 61511 and IEC 61508 standards referenced below:
SIL | Availability% | PFDavg | Risk Reduction | Qualitative Consequence |
4 | >99.99 | 10-5 to < 10‑4 | 100,000-10,000 | Potential for fatalities in the community |
3 | 99.9 | | 10,000-1,000 | Potential for multiple on- site fatalities |
2 | 99 to 99.9 | | 1,000-100 | Potential for major on-site injuries or a fatality |
1 | 90 to 99 | | 100-10 | Potential for minor on-site injuries |
- Capture Mtive and the Initial Interval will be calculated.
- Select the Done button.
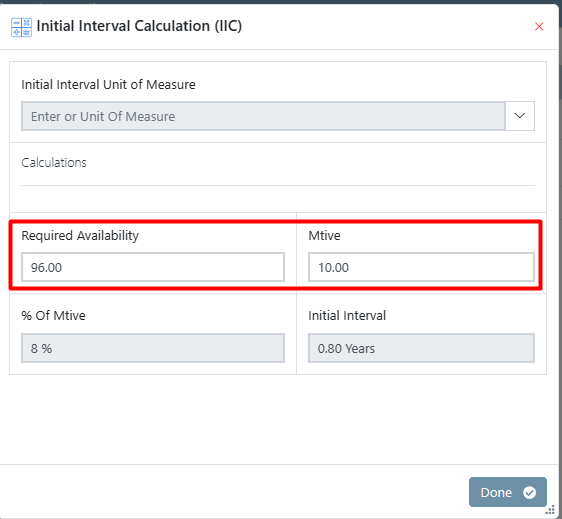

- Select the Safety Integrity Level
Calculating the Initial Interval using the Single Protective Device Method
- Select the Failure Finding button and a pop-up window will appear.
- Select a Failure Finding calculation option.
- Complete the required fields and ACTOR will calculate the Initial Interval using the built-in formulas.
- Select Done at the bottom right corner of the pop-up screen.
- Select the Standard Policy and the Standard Policy Description will automatically be populated.
- Capture the Policy Interval.
- Select the Policy Interval UOM.
- Capture the Trades.
- Capture the One-Time Changes.
- Capture additional Notes in the Notes Details section.
- Click Save.
Regulation Tasks
Quality, Environmental and Safety Standards and Regulations are being considered regarding tolerable levels of risk during the design and maintenance of assets to ensure compliance.
How to complete REG Policy Details:
- The analysis summary will already be populated with details captured in the Analysis Detail.
- The Policy Type will be pre-selected based on the answers from the Decision Diagram.
- Select the Policy Sub-Type.
- Select the Plant Status.
- Select the Equipment Status.
- Select the Regulation Code and the Regulation Code Description will automatically be populated.
- Select the Standard Policy and the Standard Policy Detail will automatically be populated.
- Capture the Policy Interval.
- Select the Policy Interval UOM.
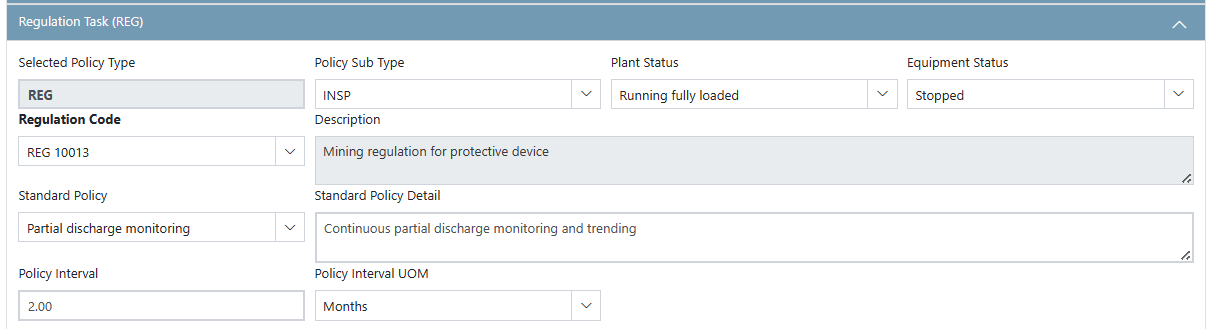
- Capture Trades.
- Capture One-Time Changes if necessary.
- Capture the Revised Risk.
- Capture additional Notes in the Notes Details section.
- Click Save.
No Scheduled Maintenance (NSM) with Optional Redesign
This entails default entails making no effort to anticipate or prevent failure modes to which it is applied, and so those failures are simply allowed to occur and then be repaired. This default is also called run to failure. NB* This does not however mean that there is no planned maintenance.
No Scheduled Maintenance is only valid if:
- A suitable scheduled task cannot be found for a hidden function and the associated multiple failure does not have safety or environmental consequences.
- A Cost-effective preventative task cannot be found for failure posing an economic risk (operational or non-operational consequences).
How to complete the NSM Policy Details:
- The analysis summary will already be populated with details captured in the Analysis Detail.
- The Policy Type and Standard Policy will be pre-selected based on the answers from the Decision Diagram.
- Capture the Standard Policy Detail
Operator Rounds or Operator Driven Reliability
Some Failure Modes identified during the RCM analysis may not be susceptible to any on condition task, scheduled restoration, or discard tasks, but are important enough to be added to the operator’s checklists. In these cases, the Failure Mode can be linked to one. These are informal tasks performed by operators during their rounds. These tasks will typically be captured on a handheld device or on check sheets.
- Check the Operator Rounds checkbox and additional fields will appear.
- Capture the Operator Round Details.
- Capture the Operator Round Interval.
- Select the Operator Round Interval UOM.
- Capture One-Time Changes if necessary.
- Capture the Revised Risk.
- Capture additional Notes in the Notes Detail section.
- Click Save.
Protection Availability Optimization (PAO) Policy type
How to complete the PAO Policy Details:
These are failure management policies developed for protective devices to increase the availability of the devices on demand to reduce the risk of multiple failures associated with this failure mode to a tolerable level and downtime after the failure management policies for protection have been optimized.
- The analysis summary will already be populated with details captured in the Analysis Detail.
- The Policy Type and Standard Policy Details will be pre-selected based on the answers from the Decision Diagram.
- Select the Protective Device Function Reference and the function will be added to the grid.
- Delete the Function by selecting the bin icon if necessary.
- Capture the Revised Risk.
- Capture additional Notes in the Notes Detail section.
- Click Save.
Compulsory Redesign (One-Time Change or COTC) Policy Type
A One-Time Change refers to any change in the specification of any item of equipment. It includes changing the specification of a component, adding a new item, replacing an entire machine with one of a different make or type or relocating a machine. It also refers to any other Once-off change to a process or procedure that affects the operation of the plant. It even covers training as a method of dealing with a specific failure mode (which can be seen as redesigning the capability of the person being trained). One-Time Changes don't only impact the consequences of the failure but may also impact the probability of the failure happening and therefore need to be considered in the task selection process.
How to complete the COTC Policy Details:
- The analysis summary will already be populated with details captured in the Analysis Detail.
- Capture the COTC Detail.
- Add a One-Time Change.
- Select the bin icon to Delete or Remove a One-Time Change.
- Capture the Revised Risk.
- Capture additional Notes in the Notes Detail section.
- Click Save.
Depending on the “Policy Type”, the form will prompt the user to capture different information. If a "Policy Type" does not support “Worth Doing” the worth doing tab will be greyed out.
Once the user has captured all the fields in the Policy Worksheet, the user must “Save” the data and the analysis is now complete. Should the user wish to change the saved decision, ACTOR will override the initial decision captured.
Related Articles
How to Complete the RCM3™ Decision Worksheet
How to Complete the RCM3™ Decision Worksheet After the Functions, Failed States, Failure Causes, Mechanisms, Effects and Inherent Risks are completed, the RCM3™ Decision Diagram is used to guide toward a failure management strategy. The user answers ...
How to add RCM Policy Types and Policy Sub-types
Policy Types The "Policy Types" are pre-configured as per below in ACTOR based on the decision matrix and cannot be changed. ACTOR does however allow users to capture Policy Sub-types that are associated to a particular "Policy Type". Adding a new ...
How to Complete the RCM3™ Information Worksheet
The Information Worksheet documents the Functions, Failed States, Failure Mode Causes, Mechanisms, Failure Effects, and Inherent Risks. The information worksheet is similar to the Failure Modes, Effects and Criticality Analysis (FMECA) where the ...
How to Complete an RCM2™ Analysis
The RCM2™ Methodology The RCM2™ methodology is a process used to determine what must be done to an asset to preserve its functions (while minimizing or avoiding failure consequences). Prior to starting an analysis, a trained facilitator or asset ...
How to Complete the RCM3™ Worth Doing Section
Worth Doing Tasks Note: If a Policy Type does not support “Worth Doing” the system will display an error message. When a maintenance task addresses an operational or economic risk, the task must be "Worth Doing." In this case the cost of doing the ...